Turning sunlight into fuel
Turning sunlight into fuel
Scientists in Germany are working on a project that will appeal to anyone living in sunny South Africa โ because, rather incredibly, theyโre turning sunlight into fuel.
Sustainable fuels are being created from water, carbon dioxide (CO2), and sunlight in a high, mirror-lined tower. Does this sound like fake news? A fairytale? A scene from a James Bond movie?
Itโs none of the above; the scenario is real. The production of fuel is happening at a project called โMaterial Advancements for Solar Fuels Technologyโ, or MAfoS for short. A team of scientists at the Center for High Temperature Materials and Design Hรถhere Technische Lehranstalt (HTL) of the Fraunhofer Institute for Silicate Research is developing advanced materials for the first industrial solar-to-fuel demonstration plant. The project is being funded by Eurostars 3, the largest international funding programme for SMEs wishing to collaborate on R&D projects that create innovative products, processes, or services for commercialisation.
A tower full of energy
The scientists have been at it for a while โ in fact, a pilot plant already exists in Jรผlich, Germany. It is operated by project partner Synhelion โ a Swiss start-up company โ using a solar tower owned by the German Aerospace Center (DLR).
In this solar-to-fuel plant, fuel is being created from water and either CO2 or methane, and the scientists are currently focusing on kerosene. The plant comprises a large area with mirrors that bundle sunlight, which is converted into heat in a tower and conveyed to a reactor chamber via a pipe. There, the heated starting products react with each other and form the desired fuel.
Special materials are required for the individual components in order to start the process and use the tower for fuel production. The combination of high temperatures and water vapour poses a challenge. At the sunlight entry window, temperatures are still relatively moderate at up to 800ยฐC, but in the subsequent process steps they increase to up to 1,500ยฐC.
Selecting material for these conditions is especially demanding, while the design solutions are complicated. New, extremely resistant high-performance coatings should make this easier in the future and provide more options for designers.
Pipes made of the oxide-ceramic composite-fibre material (O-CMC) are being used in the project. O-CMC offers high temperature stability, low density, high strength, and good corrosion resistance. This makes the material suitable for a variety of applications with demanding thermal and mechanical requirements.
High temperatures can be tricky
This is where Fraunhofer HTL comes in, with its expertise in lightweight construction and high-temperature materials. The institute is developing inorganic ceramic materials as protective coatings for various plant components and future applications.
The materials have to meet numerous requirements. For example, it is crucial for the coating on the entry window to be continuously permeable to sunlight and resistant to water vapour. In addition, the coating has to be adapted to the thermal expansion coefficient of the glass pane, so that it does not flake off during temperature changes. With the ensuing process stages and their continuously increasing temperatures, the coating must always be adapted to the corresponding carrier substrate for thermal expansion, while simultaneously remaining tight.
In addition to these materials, the Fraunhofer team is also developing carrier structures made of fibre-reinforced ceramic for pipes. Fibre-reinforced ceramic is more damage-tolerant than monolithic ceramic, but the fibres available on the market only tolerate a maximum temperature of 1,200ยฐC. The scientists at Fraunhofer HTL have set themselves the goal of achieving a higher temperature stability and increasing the application temperature of the reinforcement fibres to 1,500ยฐC.
Success is achieved
The researchers have already achieved an initial important milestone: the coating for the sunlight entry window. โThe greatest challenge here was the very low coefficient of thermal expansion. However, we have been able to identify a suitable material. Our tests were able to prove that it is not only especially resistant to heat, but also to water vapour. It protects the underlying material and is transparent enough to continuously allow enough sunlight to pass through,โ says MAfoS project manager Jonathan Maier.
In the next step, the scientists want to coat the entry window in the actual component size, so that it can be tested by the Synhelion team. Together with CeraFib, a project partner specialising in high-temperature-resistant composite materials and components, the scientists at Fraunhofer HTL have also successfully produced pipes made of fibre-reinforced ceramic.
The experts at Fraunhofer HTL are not only enthusiastic about the overall project, but also about the contribution that they can make through their participation.
โWe have always wanted to enter the field of renewable energy, energy efficiency, power-to-X, and power-to-fuel with our classic Fraunhofer HTL topics โ in other words, high-temperature coatings and materials as well as ceramic fibres,โ says Arne Rรผdinger, head of the Ceramic Fibers Department at Fraunhofer HTL. โIn this project, we are proving that we are a strong cooperation partner in this area, even for small and medium-sized enterprises, because we are customer-oriented and close to the market with our technical know-how.โ
โIt is also great that our research is able to make such an important contribution to CO2reduction and thus to the sustainable transformation of our society,โ adds Maier.
This transformation will soon be within reach: Synhelionโs industrial solar-to-fuel demonstration plant is scheduled to start operation in Germany in 2024.
Published by
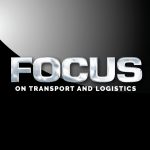
Focus on Transport
focusmagsa
