Oil the (financial) wheels
Oil the (financial) wheels
The importance of total cost of ownership (TCO) is well known – but what role do lubricants play in this equation?
Certas Energy, one of the UK’s largest independent suppliers of fuel and lubricants, summarises it neatly: “Faced with increasing pressure to improve vehicle reliability, meet safety and emissions regulatory requirements – all while minimising operating costs to remain competitive – today’s transport operators have already turned to the TCO approach.”
This method often involves monitoring the cost per km of a vehicle fleet, which includes fuel expenditure and maintenance. Certas believes that fleet operators are possibly missing out on an easy win to improve the performance of their fleet.
Not all lubricants are equal
“When looking to make savings, lubricants are often one of the first areas to be cut. While cheaper oils and greases may achieve immediate cost savings, the detrimental effect on equipment can prove to be more expensive over time.”
Effective lubrication, it adds, is key to protecting heavy-duty diesel engines, transmissions, axles and wheel bearings from the wear, deposits and corrosion that lead to frequent oil changes, increased maintenance and even component failure.
“Fuel is also a consideration and can account for as much as 39% of fleet operating costs. Therefore, a lubricant that can deliver even a small increase in fuel economy has the potential to significantly cut fleet TCO.”
Unfortunately, many transport operators don’t see things this way, as Certas explains: “A recent survey of fleet managers, commissioned by Shell Lubricants, revealed that 56% do not expect higher quality lubricants to help cut maintenance and 66% do not expect higher quality lubricants to be able to help reduce unplanned downtime.”
The survey, commissioned by Shell Lubricants, was conducted by research firm Edelman Intelligence. It is based on 395 interviews with fleet-sector staff who purchase, influence the purchase of or use lubricants as part of their job across eight countries (Brazil, Canada, China, Germany, India, Russia, UK and the US).
“When evaluating TCO it’s important to consider not only the end-to-end impact on maintenance budgets, but also any costs incurred as a result of vehicle downtime,” Certas warns.
“Factor in missed deadlines, lower vehicle reliability and reputational impact, and the true cost of poor lubrication on the bottom line can be much higher. To exacerbate the problem, once issues arise with vehicle components, the tendency is to look at grander (and more expensive) solutions over making smaller, granular changes that could create greater total cost of ownership savings.
“In fact, one in three fleet managers admit that errors in lubrication had cost their business over US$100 000, with one in five reporting costs over US$250 000. Making the decision to select a high-performance lubricant can help prevent these costs, reducing unplanned downtime and lowering maintenance costs for lower overall cost per mile.”
Certas Energy points out that a UK based road haulage business achieved over £40 000 in parts and maintenance savings by changing its lubricants for their fleet of more than 100 Iveco Stralis vehicles.
“Aware of the costly knock-on effect of vehicle downtime, this road haulage business invested heavily to avoid interruptions to service, building an on-site workshop to ensure upkeep of its fleet and introducing an annual replacement policy which means that the average age of its fleet is just three years old.
“However, after experiencing a pattern of premature turbocharger failures that forced the company to replace the turbochargers of its entire fleet every 200 000 km – as a precautionary measure – the company was facing additional vehicle downtime, lost man hours and mounting parts costs.”
A build-up of deposits from the engine oil was then identified as the cause of the turbocharger failure. And, with a recommendation from Certas, the problem was remedied when the company switched to a high-performance lubricant from Shell.
“Making what might seem like small changes to lubricant procurement can have a significant impact on TCO, but one size does not fit all,” Certas states. “Fleet managers must evaluate the needs of their business through a unique TCO approach that accounts for a holistic view of maintenance cost and vehicle downtime to realise low-cost, long-term product reliability over the lifetime of a vehicle.”
Grease also plays an important part
Andrew Hamilton, director of technical services and quality in the oil and lubricants division of CHS Inc (a global agribusiness owned by farmers, ranchers and cooperatives across the US), notes that it is extremely important to regularly grease a truck with high-quality grease.
“Grease is responsible for two things: protecting and lubricating equipment and preventing dirt and water from getting in and damaging metal surfaces,” he explains. “If grease is not regularly applied, you don’t have the constant reconfirming of the protective layer of the metal. Not only does that allow potential for wear because of lack of lubrication, but you also lack protection against the water, dirt and corrosives coming off the road.”
Hamilton says that the most important thing to know about any grease is the type of thickener that is used. “Thickeners, which are made of materials like lithium, calcium and polyurea, make grease pasty and certain thickeners are not compatible with each other.”
He adds that of the approximately 10 commonly used thickeners, about half of them are incompatible with other thickeners.
“Mixing incompatible greases will lead to ineffective lubrication, as the chemistries react with each other and disassemble. The different raw materials will begin to separate, and the greases may exhibit abnormal oil separation.
“I saw this happen in a company’s central greasing system. When they pressed the trigger of the automatic grease gun, a new colour would come out every time. Because the two greases in the system were incompatible, the base oil separated out. The lubrication materials for friction and wear separated. And the colour separated.”
Everything was still sitting in the tank, but in different layers, and it was “like looking through a kaleidoscope”.
Hamilton warns that most people get fixated on a colour. “They say, I have to have a red grease. But in fact, red greases aren’t all the same There are about a dozen different reds, but they are not all compatible. It’s about thickener and quality, not colour.”
He recommends that drivers and equipment owners use their phone to snap a photo of their grease’s label and take it to their grease supplier when purchasing additional grease.
Eliminate human error
Graco, an American manufacturer of fluid-handling systems and products based in Minneapolis, notes that even with properly times intervals, poor greasing practices and human error can result in over- and under-greasing – causing premature wear on critical components.
“Accurate, dependable lubrication is the most critical preventive maintenance step in preserving the life and productivity of any fleet,” Jack Koenig, industrial lubrication field application engineer at Graco, emphasises.
“Automatic lubrication systems provide consistent lubrication on a more frequent basis than manual lubrication. Too little lubrication creates heat and wear, while too much can create drag, heat and wear, and damaged seals.”
Charles Hartl, industrial lubrication sales manager at Graco’s Lubrication Equipment Division, adds: “The effects of under-lubrication are well known – increased component wear, premature failure, higher energy usage, and increased operating and maintenance costs. But the effects of over-lubrication are just as harmful. It wastes lubricant, leads to excess heat build-up, puts stress on lube points and increases downtime. The solution is obvious: optimal lubrication.”
Koenig explains that ideal machine and vehicle performance require maintaining a minimal lube film to separate the moving surfaces under all speeds and loads. For most grease applications, the volume of grease required is equal to an average thickness of 0,03 mm of the surface area, applied every four hours.
“For oil applications, the same thickness is applied hourly,” he adds. “Even with an acceptable variance of approximately 20%, achieving this film thickness with manual application is next to impossible. However, for metering devices in modern automatic lubrication systems, this is an easy task.”
Koenig also explains that automatic lubrication is environmentally friendly. “First, a well-lubricated machine is more energy efficient. This benefits the environment as well as the bottom line. Second, most lubricants are derived from the same crude oil used to produce fossil fuels, so using less lubricant is better for the environment. Automatic lubrication applies less lubricant more frequently, reducing waste and therefore protecting the environment.”
Automatic lubrication also increases reliability. “A manual lubrication plan can result in points being missed occasionally or forgotten entirely until something breaks,” Koenig warns. “With automatic lubrication, you can trust that the right amount of lubricant is reaching critical pivots, bearings and joints at the right frequency. Automatic lubrication systems also offer system monitoring options, alerting you to a problem with the lubrication supply.”
He adds that contaminants are also reduced. “In many operating conditions, there are natural contaminants present, which can negatively impact lubrication points and cause more wear and tear, especially when manual lubrication methods are used.”
Most often, lubrication points are not properly cleaned before manually lubricating, and the coupler used to attach to the point is often dirty too. Contaminants such as chemicals, rocks, sand and other particles are then forced into the lubrication point.
“With automatic lubrication, the grease is pumped through a filter before it enters the reservoir of the lubricator, limiting the penetration of contaminants into these lubrication points.”
Koenig says that modern automatic lubrication products help equipment owners overcome the cost penalties of conventional manual lubrication. “By applying the right amount of clean lubricant at frequent intervals and monitoring lube system performance, optimum lubrication is ensured.”
And a well-oiled vehicle will run more efficient for longer, benefiting the TOC and bottom line.
Published by
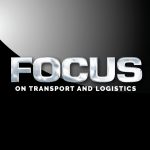
Focus on Transport
One Comment
Leave a comment Cancel reply
focusmagsa

Lubricants have specifications – either they meet them or they don’t. You don’t rate lubricants according to their price. IOW, you don’t get expensive or cheap lubricants of the same specifications. They all more or less the same price.