MAN’s etruck: destined for the N3?
MAN’s etruck: destined for the N3?
MAN is charged and ready to go! With the development of its eTruck, the manufacturer has solved the problem of long-distance battery-electric trucking. In theory. As CHARLEEN CLARKE writes, many challenges lie ahead…
Picture the scenario: the N3 is populated by electric trucks. They’re everywhere. Silently, efficiently, and in an environmentally friendly manner, they ply their trade on the country’s busiest trucking route, delivering the goods and offering operators a low total cost of ownership (TCO) to boot.
At the moment, that’s akin to a magic carpet ride: it’s not going to happen now, nor any time soon. The truck manufacturers are not to blame, though. They’re launching electric trucks almost as fast as you can say “e-mobility”.
Take the latest – and arguably greatest – electric truck to glide silently onto the transportation horizon: MAN’s eTruck. The company has done a stunning job of developing and building prototypes of these vehicles. Some 20 eTruck prototypes have been built at MAN’s eMobility Centre, located at the manufacturer’s main plant in Munich.
In future, the eTrucks will be built on the same lines as their diesel-engined siblings. The company has been training up a storm (it’s obviously a completely different kettle of fish to build electric trucks versus those with internal combustion engines); by the end of 2023 all relevant skilled workers in truck production will be qualified for the series production of electric trucks. Meanwhile, the company will be producing around 100 000 battery packs a year at its Nuremberg plant from 2025.
Recently, we travelled to Munich to test drive near-production prototypes of the new electric truck, which will be launched in 2024 – and it is super impressive. Alas, the infrastructure that needs to go hand-in-hand with the truck isn’t quite as inspiring…
More about that later. Let’s start with the positive stuff: our experience of the eTruck and everything we currently know about it. The driving experience is nothing short of sensational; acceleration is seamless and ever so smooth. As is normally the case with an electric truck, the low-down torque is staggering; I could not help but let out a little giggle after flooring the accelerator and racing forwards.
We cannot comment on the interior of the vehicle: we were asked not to photograph it because the trucks are prototypes, and the serial trucks could look quite different. We don’t expect to have any complaints in this regard, as MAN’s interiors are exceptional.
The batteries are, of course, one of the most important components of the eTruck. It was therefore interesting to learn that the eTruck is using MAN’s third generation batteries (the first generation was used in the MAN eTGM and the second in the MAN Lion’s City E city bus, which has achieved over 550 kilometres on one battery charge).



Speaking of range… it’s one of the burning questions with the eTruck. The other is charging. The charging statistics in the technical specs require some clarification because I honestly cannot reveal the range of the truck (we were not given this information). Instead, we were told that daily ranges between 600 and 800 km are possible, while a daily range of up to 1 000 km daily will be achievable in the second half of this decade with future battery generations.
However – and this is a very important proviso – this assumes that the driver will stop to charge the truck, because it cannot do 600 or 800 km on a single charge (which is the belief held by some operators).
By law, truck drivers in Europe must take a 45-minute break after every four-and-a-half hours at the wheel – so the stop is a given. When the driver stops, though, they will need to locate a Megawatt Charging System (MCS) – and not a conventional Combined Charging System (CCS) rapid charger.
MCS operates at a voltage of up to 1 250 volts and uses its own plug design. However, the key difference is the charging performance. CCS can provide a maximum of 375 kW, while the first phase of MCS can offer 750 to 1 000 kW. In theory, up to 3.75 megawatts will be possible, hence the name of the system. That is likely to be needed under some circumstances at a later date for coaches that travel at higher speeds and have less time available to charge.
The challenge is that the eTruck also needs to be able to fill its batteries quickly. By the end of the break, the power reserves of the eTruck should be full again – so MCS is vital.
So, in order for the eTrucks to work over long distances, a network of megawatt chargers needs to be in place. There are lots of initiatives underway to build up that network in Europe. For instance, MAN is part of a joint venture which aims to create a high-performance charging network in Europe with 1 700 green electricity charging stations.
But the network doesn’t currently exist. Neither does a ready and reliable supply of green electricity.
It would also be handy to have lots of parking bays for trucks that are equipped with CCS chargers. Therein lies another challenge: there aren’t enough parking bays for trucks in Europe (some say the shortage totals around 40 000) and the bays that do exist don’t have chargers.
This brings me back to the N3 and sunny South Africa. There are a number of reasons why we won’t see thousands of eTrucks trawling up and down the N3 any time soon. Firstly, there is the issue of cost: by the middle of this decade, e-mobility in Europe will be cost-neutral compared to diesel vehicles from a total cost perspective. The significantly higher acquisition costs for the battery-electric vehicle will be compensated for by the reduction in variable operating costs (energy, toll, etc). South Africa is a highly price-sensitive market, though, where there are no incentives or compensations in place. Big problem.
Secondly, we don’t have a network of chargers – forget about whether they’re CCS or MCS. The establishment of that network will cost a small fortune. Who is going to foot the bill?
Thirdly, we don’t have a steady supply of green electricity. Goodness gracious, we don’t even have a steady supply of dirty electricity.
The fourth problem is product related: the initial focus is on 4×2 and 6×2 models; 6x4s will only come in 2027 or 2028.
So, we have challenges. Huge challenges, in fact. Are they insurmountable? I really hope not, because I’d love to see that magic carpet ride become a reality.
Above: MAN’s eTruck will be market ready in 2024.
Specifications of our test truck
Model: New MAN eTruck 4×2 LL SA (prototype)
Type: 4×2 tractor for long-haul application with low chassis height
Engine: Permanent synchronous motor
Batteries: Lithium-ion battery packs made by MAN, with 300 to 500 kWh usable battery capacity
Battery charging: CCS charging up to 350 kW / preparation for MCS charging; Recuperation during engine braking for longer driving distance
Power: Serial range will be from 300 to 350 kW
Torque: More than 3 000 Nm
Transmissions: Two or four-gear transmission
Cab: GX
Gross combination mass: 40 000/42 000 kg
Driving range: Daily range of between 600 and 800 kilometres
Emission: Zero emission, zero CO2, zero NOx
Application: Long-haul volume transport
Going electric? Check this out first
While in Munich, we were introduced to MAN’s eReadyCheck app, where you can find out which routes can be electrified – and it’s really remarkable. Operators enter certain parameters (range, truck, application, payload, temperature, roads, intended trips) and the app recommends the ideal electric truck for your needs. It also tells you how many battery packs are advised, what range you will get, and what your charging time will be.
It’s utterly fascinating stuff and, given the move to new technologies, we reckon it’s super handy too. It’s a free tool for operators – so you can “play” with it to your heart’s content.
Still confused as to which way to go? The company has employed a small army of technical experts who will consult with operators when it comes to anything and everything to do with e-mobility – from the most suitable routes to required charging infrastructure. Very importantly, they will also provide guidance when it comes to battery management (which, of course will be a decisive factor for the economic efficiency of vehicle operation in the future). The experts will make use of a sophisticated Battery Analytics System, which has been specially developed at MAN.
According to the technical experts in Munich, this service has been provided free of charge “in order to guide the customer through the jungle of questions”.
So there you have it. E-mobility. Done and dusted.

Above: The International Truck of the Year jury was invited to Munich to test drive prototypes of the eTruck.
Hydrogen: the next big thing?
We’re often told that battery-electric vehicles (BEVs) are ideal for inner-city distribution while long-haul is exclusively the terrain of fuel cell electric vehicles (FCEVs). Is this true? The experts at MAN don’t necessarily agree…
They point out that – in addition to the initial investment – cost of fuel, energy efficiency, maintenance costs, and the charging or refuelling infrastructure need to be considered.
While FCEVs have use cases in specific applications and hydrogen is an abundant energy source, the experts say other factors – such as the cost of fuel cells and hydrogen tanks and refuelling infrastructure – make battery-electric the most cost-effective option when considering total cost of ownership. Furthermore, series readiness and load capacity of FCEV drives are not yet comparable with the other drives.
Electric drives are less maintenance intensive than both internal combustion engines (with their many parts) and hydrogen vehicles (with their fuel cells, gas tanks, and numerous additional lines).
What about energy costs? During operation, we were told, BEVs are the most economical alternative. BEVs also have an advantage over hydrogen trucks in terms of energy efficiency: with BEVs, 75% of the energy flows into the drive, while with FCEVs this drops to 25%.
When it comes to procurement costs, vehicles powered by hydrogen fuel cells are between 2.5 and three times more expensive than commercial diesel vehicles, whereas battery-electric vehicles are only about twice as expensive. A Traton Group internal study has predicted cost parity of BEVs for all application segments by 2025 at the latest. To achieve cost parity, the price of hydrogen would need to be around €3.10/kg, but the forecast for 2030 is between €5.00 and €7.50.
* Subsidies and tax reductions can positively influence the purchasing price.
TECHNICAL DATA: FULL eTRUCK RANGE
4 x 2 Solo chassis | 6 x 2 Solo chassis | 6 x 2 Chassis with trailer | 4 x 2 Semitrailer combination | |
Weights | Gross train weight up to 20 t (legal/technical) | Gross train weight up to 28 t (legal/technical) | Gross train weight 42 t | Gross train weight 42 t |
Engine power (approx.) | 200 to 230 kW | 200 to 230 kW | 300 to 350 kW | 300 to 350 kW |
Usable battery capacity (approx.) | 200 to 500 kWh | 200 to 500 kWh | 200 to 500 kWh | 300 to 500 kWh |
Published by
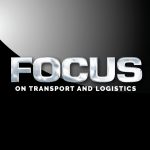
Focus on Transport
focusmagsa
