Digital technology key to business success
Digital technology key to business success
Telematics, connectivity, data analysis… digitalisation and automation are providing logistics companies with an array of options to keep their businesses economical and environmentally friendly.
The logistics industry is facing enormous challenges. From cost pressures, to increasing customer expectations when it comes to sustainability, or international competition for evermore valuable drivers, remaining successful in this business is becoming increasingly difficult the world over.
Adding to these issues, competition in the transport industry is also changing: large shipping agents and online retailers who used to be transport customers themselves are now developing their own logistics infrastructure. In some studies, logistics experts are predicting these new competitors will become even more important than ship- or rail-based transport.
If logistics companies don’t want to miss out, they need to find ideas and solutions for transporting goods from A to B while still making a profit; digitalisation and automation can be of assistance here. While automated high-bay storage systems are already par for the course for any progressive logistics firm, automation on the road – for instance in the form of automated motorway driving or automated vehicles at the depot – has not reached its full potential. In contrast, logistics companies are already able to generate a range of positive benefits for their business through digitalisation.
Logistics moves to digitalisation
Compared to businesses in other industries, logistics companies tend to already employ a relatively high degree of digitalisation. Be it in the warehouse, during the transport process, or in the office, almost every area of the logistics sector is going digital. Warehouse management systems, digital fleet management tools, and digital signatures are particularly commonplace.
The efficient, cost-effective, and sustainable combination of warehouse management and scheduling of truck and trailer movements is the key skill required by every quality-focused logistics and transport provider. Modern telematics systems provide schedulers and drivers with all relevant data from the truck and trailer in real time. This offers a wealth of benefits: data can be used to help drivers to improve their driving style, saving fuel and CO2 as a result; routes can be planned for maximum efficiency; vehicles can be sent to the workshop on time for maintenance or can even issue automatic warnings about potential future damage (predictive maintenance).
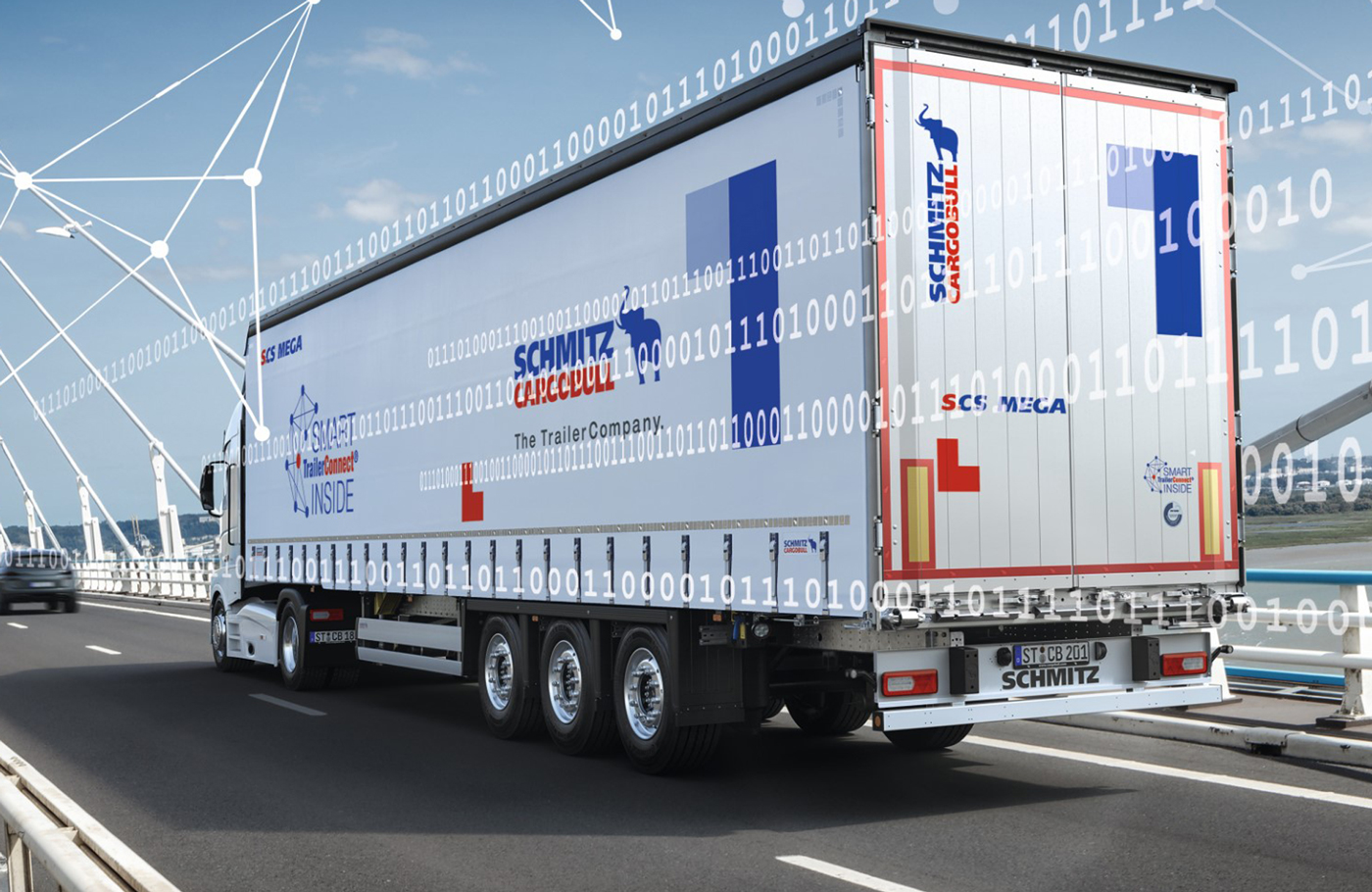
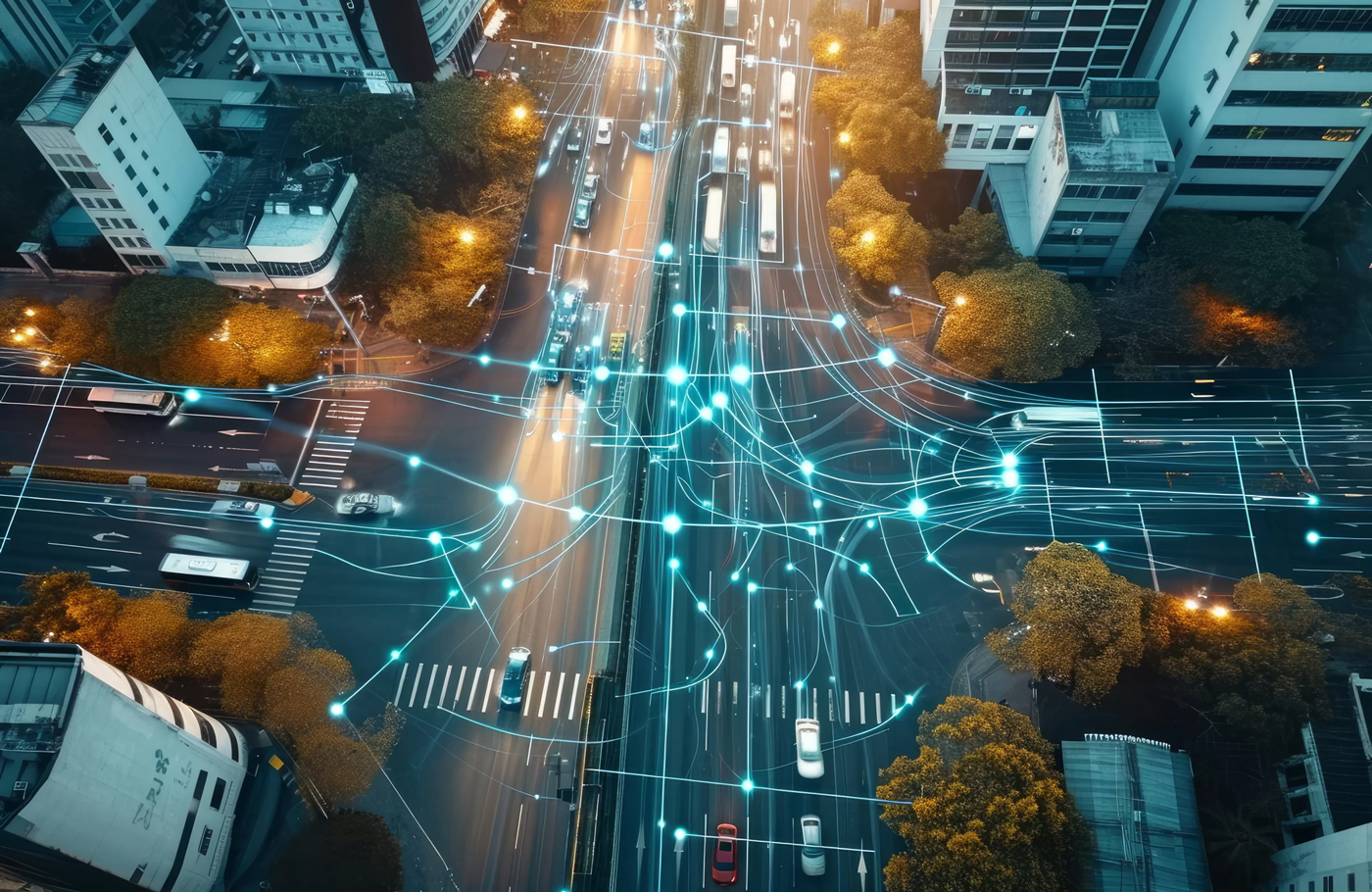
Networking adds value
Customers and schedulers can receive real-time information on the arrival and condition of goods. The use of digital tools to permanently monitor the cold chain and trailer – particularly for refrigerated goods and pharmaceuticals – provides valuable assistance when it comes to complying with statutory cooling requirements or preventing theft and vandalism. These benefits have long spread far beyond the logistics companies themselves. Now, modern interfaces enable freight agents and shipping companies to connect with one another and transfer transport jobs from one transport management system (TMS) to another without any problems.
For many years, companies such as Schmitz Cargobull have been digitalising their products for the benefit of their customers. For instance, the S.KO COOL refrigerated semi-trailer is not only equipped with Schmitz Cargobull’s own TrailerConnect telematics system as standard, it also meets the requirements of the TAPA TSR1 standard for security equipment in refrigerated trailers, thanks to a digital acoustic alarm system and an electronic door locking system to protect goods inside the trailer.
Closely modelled on the S.KO COOL, the fully electric S.KOe COOL is fitted with the electric cooling unit, the S.CU ep85, which extends the running time with energy regenerated by the installed electric axle and also reduces the time needed to recharge via the mains grid. Importantly, the telematics portal can be used to monitor the status of the system (charge status of the battery, remaining range, remaining charge time, and so on).
An intelligent battery charging management function also ensures that the battery charge level remains as high as possible to provide greater reliability when the trailer is stationary (in traffic jams, for example). Thanks to three pre-defined modes (Eco, Standard, and Safe), the trailer can be optimised directly by the scheduler according to the customer’s usage conditions and objectives.
Other suppliers to truck and transport companies are also increasingly digitalising their products to enhance efficiency, safety, and sustainability. An example of this digital transformation is the adoption of smart fleet management systems by parts suppliers and manufacturers. These systems integrate IoT (Internet of Things) sensors, telematics, and advanced analytics to provide real-time data on vehicle performance, driver behaviour, and maintenance needs.
Tyre manufacturers, for instance, are embedding sensors within tyres to monitor pressure, temperature, and tread wear. Michelin offers a digital tyre management system called Michelin Track Connect for passenger vehicles and Michelin Tyre Care for commercial fleets. Continental, meanwhile, has developed the ContiConnect and ContiPressureCheck solution.
These smart tyres communicate data to a central dashboard accessible by fleet managers. The system can predict tyre wear, alerting managers when replacements or rotations are needed, thereby preventing blowouts and reducing downtime. This predictive maintenance approach not only ensures safety but also optimises tyre lifespan, leading to cost savings.
Similarly, brake system suppliers are incorporating digital monitoring tools that provide data on brake pad wear, heat levels, and overall braking efficiency. Real-time data helps in planning maintenance schedules and avoiding unexpected failures, improving both safety and operational efficiency.
One example is Bosch, which offers advanced Brake Pad Wear Sensors and digital brake management systems that provide real-time information on brake pad condition and wear levels. These systems use sensors to detect when brake pads need replacing and transmit this information to the vehicle’s onboard diagnostics (OBD) system or directly to fleet management software, improving maintenance planning and reducing downtime.
Furthermore, digital twin technology is being employed by suppliers of engines and powertrains. By creating a virtual replica of a truck’s engine, suppliers can simulate performance under various conditions and predict potential issues. This data is then used to refine engine design, improve fuel efficiency, and reduce emissions, aligning with sustainability goals.
Overall, the digitalisation efforts by suppliers enable truck and transport companies to move from reactive to proactive maintenance, optimise operational costs, and enhance driver and vehicle safety. These digital tools provide a comprehensive view of the fleet’s health, allowing for better decision-making and improved service delivery.
Published by
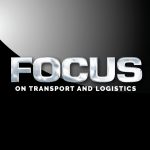
Focus on Transport
focusmagsa
