Cleaner engines – better protection

Many original equipment manufacturers (OEMs) are extending service intervals to double what they once were. The question is: how have extended motor-oil drain intervals been made possible, and is there anything that fleet managers need to know?
Motor oil is used to reduce friction and prevent engine wear, as well as to displace heat and control contaminants. There are two major components that go into oil; the first is the base oil and the second is the additive package.
The best “long-life” motor oil is synthetic, and uses the highest quality base oils with additives that enable the oil to be used for longer, while still providing superior lubrication. “Long-life” additives are designed to attach to (or neutralise) contaminants such as dirt, acid content, soot and metallic particles. As they do this, they become heavier and settle, or are separated from the oil in the filter.
One benefit of using long-life motor oil is the potential to save on running costs including parts and labour, as well as the environmental benefit of lowering resource use. However, John Evans, diagnostic manager at WearCheck, says: “The biggest savings are derived down the line with an overall reduction in downtime and therefore increased asset availability.”
Dominic Rimmer, technical services executive of Isuzu Motors South Africa, says: “Extended service intervals talks to our vision and our mission in terms of delivering the best customer experience and recognising the impact on the environment.”
Many OEMs list specifications for both long-life and standard service motor oils in their service handbooks. In markets like Europe, where environmental legislation is more stringent, and fuel quality is better, consumers are required to use long-life alternatives.
Evans says: “In South Africa, any decision to alter drain intervals must take into consideration OEM warranties, engine design, maintenance schedules, vehicle application, fuel quality and the operating environment.”
Developed in partnership
Lubricant manufacturers do not work in isolation. Steffen Niemietz, research and development application engineer at Liqui Moly Germany, says: “OEMs work with oil manufacturers to develop oils with additive packages that satisfy the demands placed on them.”
Rimmer elaborates: “In support of the service intervals implemented for our products, all affected components are designed and validated accordingly. This includes all service parts, lubricants and fluids.
“During validation testing, lubricants are sampled and analysed regularly, and all service components are carefully monitored. This ensures that all the parts and lubricants continue to perform as expected until it is time for the next service.”
What operators need to know
There is a limit to the amount of additives that can be added to a blend of oil, because many are metallic-based and may cause damage if used in a high concentration. Also, additives are sacrificial in nature, which means they get used up over time and must be replenished.
Evans says: “Application probably has the biggest influence on the lifespan of the oil. It is important to be aware that if the application changes, then the acceptable oil drain period may also change. For example, dirt is extremely abrasive and vehicles operating in dusty conditions should have their oil analysed more regularly.
Yet another misconception inherited from the past is that it is necessary to allow a vehicle to warm up before use. Advances in engine design and engine efficiency have rendered this practice outdated. In fact, starting a vehicle in the morning and allowing it to idle for ten or fifteen minutes will lead to fuel contamination or dilution of the oil.
This is because, while cold, the engine management system is designed to deliver more fuel at idle. “This ‘over fuelling’ condition may result in fuel mixing with oil in the sump. This reduces the viscosity of the oil and its load-bearing capacity or ability to adequately lubricate the engine,” explains Evans.
Long-life additives
“The main lubricant factors that need to be controlled when extending oil-drain intervals are oxidation, wear, acid content and soot contamination; and it is often the soot content that is the limiting factor,” says Evans.
Oxidisation occurs when the base oils react with oxygen in the atmosphere. Evans explains: “As a general rule of thumb, every ten-degree rise in temperature doubles the amount of oxidation and halves the lifetime of the oil.” An antioxidant additive is added to retard this process, but this, too, is depleted over time, even under ideal operating conditions.
According to WearCheck the quality of diesel in South Africa is poor and this results in a larger amount of combustion by-products that end up in a vehicle’s oil. “The sulphur content of most of the fuel currently sold in South Africa is higher than that found in many other countries. When the sulphur is burnt during the combustion process it forms a variety of acids – one of these is sulphuric acid, commonly known as battery acid, which is disastrous to engines,” says Evans.
Another problem with some fuels available locally is that of soot. Dispersants are additives that are blended with the oil to control soot. Evans says: “Most seal materials are incompatible with the dispersant chemicals, which also cause the oil to thicken at low temperatures. This produces more soot, which causes an increase in oil viscosity.”
While oil-drain periods can safely be extended, the period is limited by external factors like the quality of fuel used and the application of the vehicle. As such, it is best to discuss any changes with the OEM before any decision is made. “The most important question to ask is: Will it save me money in the long run?” concludes Evans.
Published by
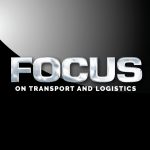
Focus on Transport
focusmagsa
