Back to the basics of transporting petrochemicals
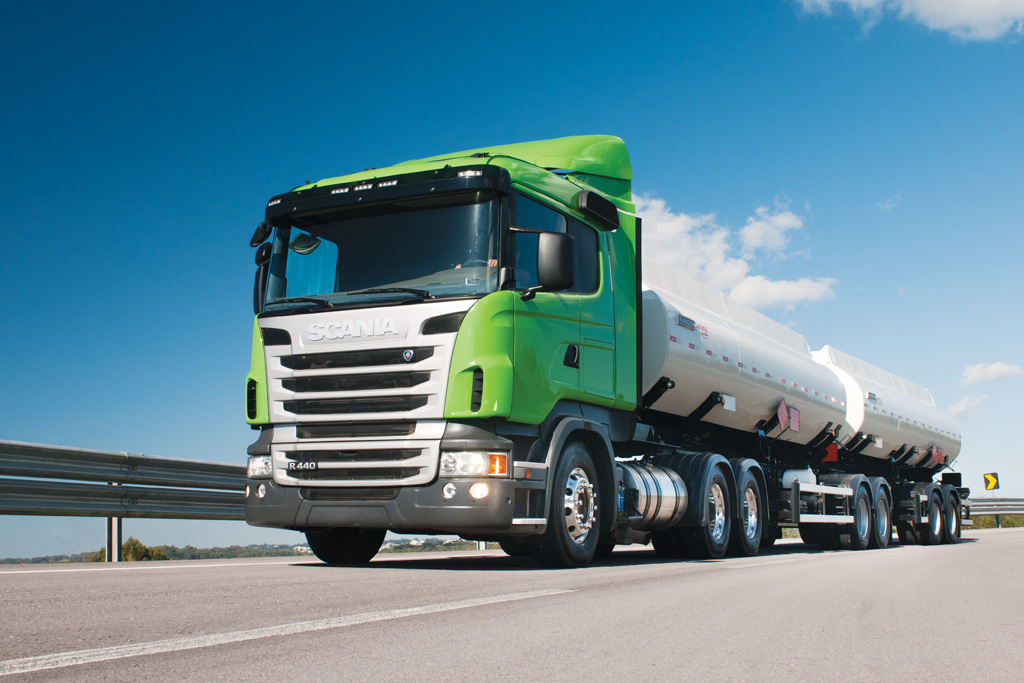
Covering the basics is always the most important aspect of approaching any big task, and hauling dangerous petrochemicals across a country or continent is no exception. FOCUS looks what companies should consider when transporting petrochemicals.
The petrochemical industry in South Africa is estimated to make around R365 billion a year in sales. It is a large, profitable industry that is vital to the country. Just as important – and possibly just as profitable – is the transport of petrochemicals, which requires important preparation in order to secure the safety of the driver and the environment.
Good preparation is the only defence a company has in avoiding expensive spills. As with any grand task, it all starts with the necessary planning and regulations.
Guiding regulations
Regulations for transporting dangerous goods and petrochemicals apply to the vehicle, handling of the material and the driver.
All drivers transporting dangerous goods need to be 25 years old, with a category-D professional driving permit (PrDP). They are also required to be certified annually as a “qualified person” by a training provider that is accredited by the Department of Transport (DoT). This ensures that only the most qualified and experienced drivers handle dangerous goods on South African roads.
Transport companies also need to fully understand and comply with the Dangerous Goods Regulations and a variety of relevant South African National Standards (SANS) as determined by the South African Bureau of Standards (SABS).
The standards are reviewed every two years, which could lead to changes as technology develops and incidents occur. A standard could also be removed if it is no longer applicable. Eddie Crane, MD of Dangerous Goods Regulations (DGR) Compliance Solutions, explains that non-compliance with regulations is often due to negligence.
“Sometimes these mistakes occur because people are not aware of the legislation. However, in many instances it is just due to negligence. Companies might have been transporting dangerous goods in a specific way for many years and decide not to change when new legislation is introduced,” he says. This would, however, be a mistake as many insurance companies will not reimburse a non-compliant transport operator if an incident occurs.
Vehicle fitness
Aside from regulations stating how the goods need to be transported, handled and packaged, the vehicle itself also requires quite a few additional features. These include placards indicating the transport of hazardous material and a Dangerous Goods Transport Permit, which is issued by a local emergency responder.
Simply having the necessary placards and documentation on board the vehicle is not enough, however. Crane states: “Placards must be displayed with a ten-millimetre black border to ensure all the relevant information is visible. Many transport operators will put the placard in a small frame, which wouldn’t show the black border. A company can be fined if the border does not show.”
“Another mistake made by operators is incorrect labelling of the container holding the dangerous goods. The transport of blood is a key example. If, for instance, the blood is HIV positive, it could have a knock-on effect on anyone else who comes into contact with it,” Crane says.
Similarly, a company can be fined if the documentation on board is not up to standard. Crane uses the emergency card as an example. The card should have a red border and be on an A4 page. When companies receive the card from a third party, they often photocopy the pages to black and white. According to Crane, these documents are no longer legal.
A vehicle should also have all the necessary safety equipment on board at all times. This includes a fire extinguisher and spill kit to ensure the driver can adequately respond to any possible fire hazard or spill. It is important to include a spill kit that is specifically designed to absorb the particular chemical being transported.
There are various spill kits available for different materials ranging from oils and fuels, bodily fluids and biological waste, to mercury and glass shards (for more information on spill kits see FOCUS Issue 7 of 2017).
Equipping the driver
Drivers should be familiar with the route and should frequently check the condition of the vehicle. Transport operators should also equip drivers with the correct personal protective equipment such as safety boots, face shields, overalls, hard hats and reflective clothing when travelling at night.
In addition to category-D PrDP training, a driver should also receive further training from the DoT. Drivers should be able to use all the onboard safety equipment efficiently. It is advisable for drivers to have training in firefighting, spill response, first aid and the handling of the specific dangerous goods being transported.
“One of the most common mistakes that occur in the transport of dangerous goods is the lack of driver training. Drivers of vehicles carrying dangerous goods are not receiving specific training in the cargo that they are transporting; they are receiving only general training,” Crane says.
Other employees involved in the transport of the dangerous goods, such as the supervisor, should also receive training. This is, however, a common oversight.
Crane advises: “Operators transporting dangerous goods should attend a management seminar or training course. Companies such as DGR Compliance Solutions offer all the different levels of training suitable for managers through to drivers.”
With a properly trained driver and a vehicle fitted with equipment that complies with the regulations, together with relevant insurance and an awareness of the latest changes to regulations and standards, transport operators should be ready to drive through 2018 with confidence.
Published by
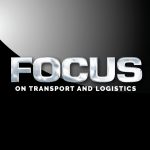
Focus on Transport
One Comment
Leave a comment Cancel reply
focusmagsa

Transporting petrochemicals is extremely dangerous so it’s very important to have a vehicle on the right conditions.