The changing face of warehousing
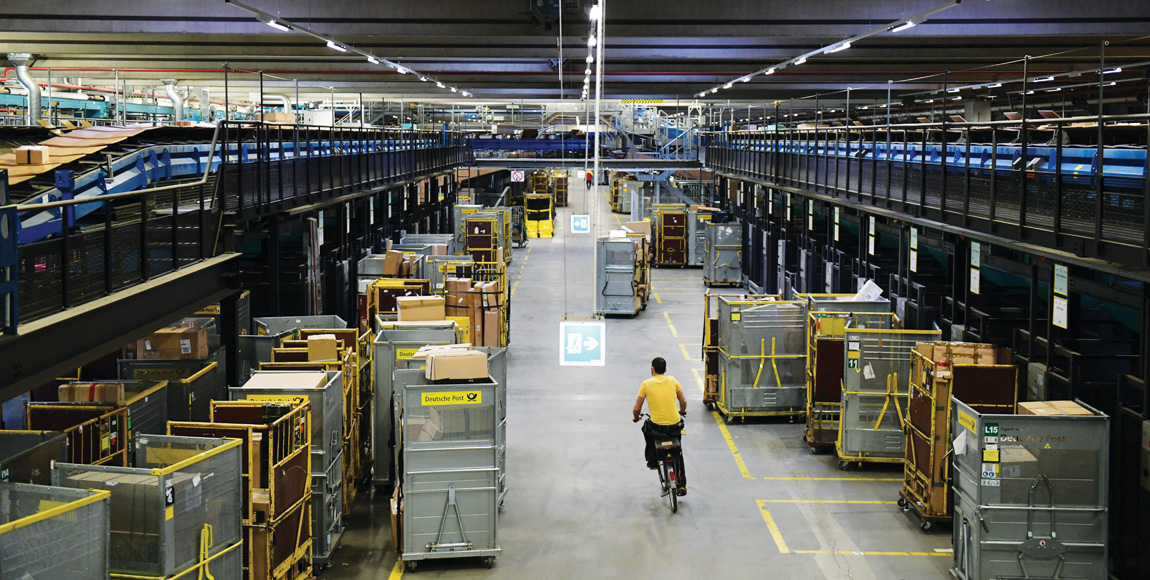
The introduction of augmented reality, artificial intelligence (AI) and robotic systems are among the many digital tools that are beginning to change concepts of warehousing in the service parts logistics sector
According to a recent study by the Service Logistics Division at DHL, digital tools aimed at boosting worker productivity, increasing speed and reducing errors are beginning to revolutionise the way service parts warehousing works.
In the evolving warehouse – equipped with 5G and high-speed Wi-Fi connections – staff members will be guided by augmented-reality glasses to correct stock locations for order picking or replenishment activities, while digital communication tools – such as video-conferencing systems or live-feeds from body cameras – will help companies to manage service parts divisions more effectively.
“A warehouse worker receiving a returned part of unknown condition or origin will immediately be able to call on advice from a remote expert to ensure the item is correctly identified, classified and sent on for repair or recycling. That expert might even be an AI assistant,” the study says.
It adds that recently introduced technology already allows parts to be compared – using high-resolution photographs taken at the time of production, for example – to enable manufacturers to establish whether the returned items are within warranty, or to spot counterfeits.
According to the study, some aspects of the warehouse of the future are already with us, robotic systems having made their way into high-volume, high-throughput retail and e-commerce facilities. “As robotic picking systems continue to become cheaper, more capable and more flexible, they will become viable options for service parts logistics environments, too,” the study predicts.
It points out that the service parts logistics industry could also provide the elusive answer for additive manufacturing. “The capabilities of three-dimensional printing technologies are continually improving, handling a wider range of materials, producing a wider range of geometries and operating at higher precision. That paves the way for many more types of parts to be built on demand, either at dedicated facilities or even in micro factories, embedded in warehouses or forward stock locations.”
According to the study, the final stage of the service parts logistics chain presents significant opportunities for companies to differentiate themselves from competitors and tailor their offerings to suit specific customer needs.
“Service logistics operations may benefit from innovative approaches now being pursued by e-commerce companies. If an area has sufficient aggregate demand, shared, collaborative or crowd-sourced last-mile transportation strategies can combine rapid response with low cost and a small carbon footprint,” it says, adding that automated lockers used for unattended e-commerce deliveries have already been adapted to hold vendor-managed inventory and consignment stocks of parts at customer sites.
“Delivery to vehicle approaches, guided by global positioning system trackers, could boost the productivity of service technicians, allowing them to receive parts for future jobs while they are working on earlier ones.
“In the longer term, drones or autonomous ground vehicles may become viable delivery systems for some categories of parts.”
Another innovative solution highlighted in the study involves virtual technicians – a role that DHL believes will be unique to the service parts logistics process, which often requires the schedules of technicians and parts deliveries to be closely aligned.
“Augmented reality systems and AI-powered personal assistants may help couriers or end customers to perform some service tasks themselves. For complex and safety-critical service tasks, skilled and properly qualified technicians are an essential, but often limited, resource.
“Advanced planning and scheduling systems will help to maximise the availability and productivity of the field workforce by dynamically adjusting job sequences and parts deliveries based on real-time information,” the study concludes.
Published by
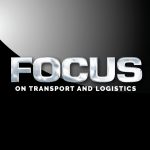
Focus on Transport
focusmagsa
