Shell proves how efficient trucks can be

Shell has been in the news a lot lately for its forward-thinking stance on the future of mobility – and it has just gone one star-lined step further…
The company has teamed up with the Airflow Truck Company to develop the Starship: an “innovative, material step towards reducing emissions and increasing overall efficiency and fuel economy in the transport sector”.
The mission was to develop a hyper-aerodynamic, super fuel-efficient, heavy-duty concept truck capable of instilling the best of today’s existing and custom technologies, with the end goal being to find out just how energy efficient goods transport by road can be today.
The results immediately proved encouraging… The Starship’s energy optimising properties were showcased during its maiden 3 700 km cross-country test stretching from San Diego, California, to Jacksonville, Florida, where real-world conditions were experienced.
The vehicle’s gross weight measured 33 112 kg, with the payload (clean reef material destined for new offshore reef installation in Florida) weighing 18 098 kg.
This American coast-to-coast run resulted in the team attaining a consumption figure 68,9 tonne-kilometres per litre in freight-tonne efficiency (FTE) – 2,5-times better than the North American average of 27,8 tonne-kilometres per litre.
Additionally, Starship’s total average fuel economy stood at 3,8 km/l, beating the American average of 2,7. The best fuel economy attained during the drive was 4,2 km/l. These measurements were verified by an independent third party, the North American Council for Freight Efficiency, using an onboard telematics system.
It has been estimated that if all two-million trucks in the United States reached the overall fuel economy and FTE performance of Starship, there would be 229-million tonnes less of CO2 emissions each year.
How were these stellar results achieved? The teams focused on enhancing various aspects of the vehicle including advances in engine and drivetrain technology, the use of low viscosity synthetic lubricants, aerodynamic designs and efficient driving methods.
“The pursuit of significant fuel economy gains for heavy-duty vehicles is a challenging process, given the immense size of the vehicle, coupled with the traditional construction of both the tractor and the trailer,” explains Robert Mainwaring, Shell Lubricants Technology manager for innovation.
“However, with new emissions regulations on the horizon, and the increasing demands of customers calling for improved efficiencies, we realised that the need for innovative thinking is imperative.”
The aerodynamics of the trucks were enhanced with a bespoke hyper-aerodynamic cab made entirely out of carbon fibre. The front-end features active grille shutters to maximise aerodynamics when engine cooling is not required.
The rear of the trailer makes use of an aerodynamic boat-tail addition, making the truck streamlined and reducing its drag coefficient. Further, elongated side panels maintain airflow with the long side skirts that reduce rear-end drag.
An automatic tyre inflation system ensures consistent tyre pressure for optimal fuel economy, while a down-speed axle configuration uses advanced engine controls and an automated manual transmission to provide improved efficiency as well as good pulling power.
To ensure that the vehicle makes use of as much renewable energy as possible, a 5 000 W solar array on the trailer roof charges the main 48-v battery bank on the tractor.
This battery bank powers the cab air-conditioning and inverter for the 120 v hotel loads. When down-converted to 12 v by a cab-mounted DC-to-DC converter, it will power the normal truck electrical components such as lights, wipers, blower motors and gauges.
The company comments that a hybrid-electric axle system is yet to be installed with an electric motor and axle replacing the non-driven rear axle of the tractor. This system will inevitably provide a power boost on inclines, where the most fuel is consumed.
Further, the hybrid axle uses regenerative braking to charge the battery pack by capturing energy while decelerating, or while descending a hill.
Shell’s expertise came in providing detailed technical consultation on engine and drivetrain components during the planning and production phases of the Starship initiative, as well as recommendations on which lubricant would provide optimal results.
Making use of Shell’s next-generation, low-viscosity, fully synthetic, heavy-duty engine oil, the use of fully synthetic base oils, plus advanced additive technology, provides Starship with improved protection against wear, deposits and oil breakdown, while improving fuel economy. The lubrication technology shares the same viscosity as Shell Rimula Ultra E+ and is being tested by original equipment manufacturers (OEMs) around the world.
Moreover, Starship uses fully synthetic Shell Lubricants including Shell Spirax S6 GXME 75W-80 transmission oil, Shell Spirax S5 ADE 75W-85 differential oil and Shell Spirax S6 GME 40 wheel-hub oil.
“We are proud that the Starship Truck was able to complete the coast-to-coast run in real-world trucking operations and conditions, including torrential rains. Our goal with this initiative is to challenge how the trucking industry defines trucking efficiency and enable further discussions with AirFlow Truck Company and other manufacturers,” remarks Mainwaring.
“What we have learnt so far is nowhere near the final result; it is simply the start of our ongoing learning. We’ll move forward to apply what we have learnt from this test run and implement additional technologies on the truck for future testing.
“While it would be easy to say the Starship initiative has been very successful, we know there is more we can do to continue to drive industry dialogue in the future,” he concludes.
Published by
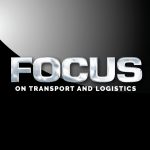
Focus on Transport
focusmagsa
