Can it carry the load?
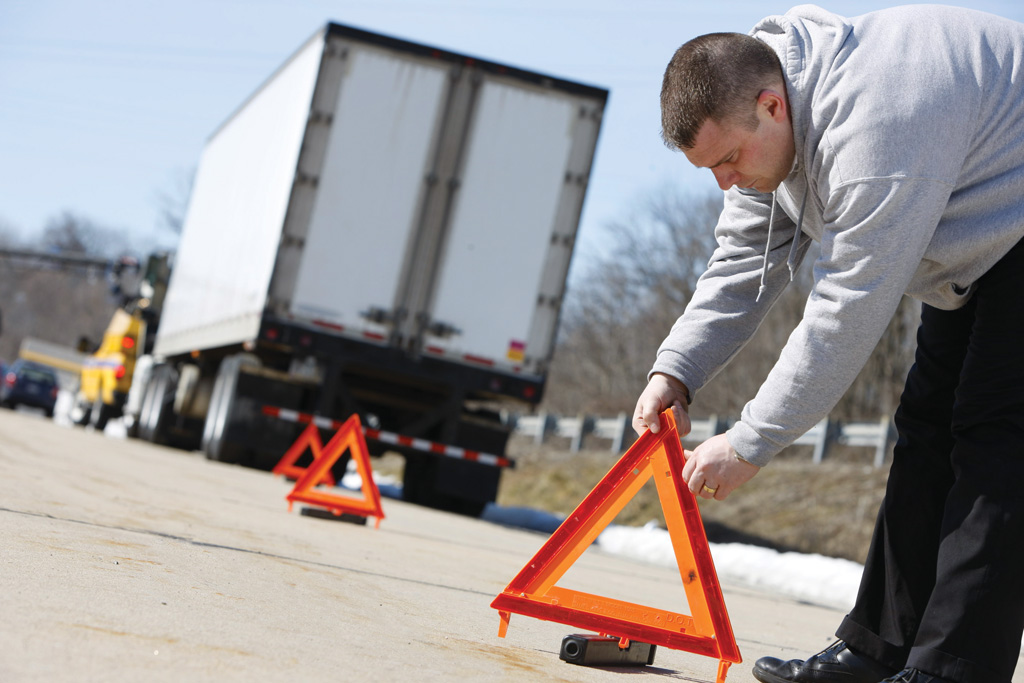
The maintenance of a vehicle will differ depending on its application, age and condition. However, there are some basics that apply to all vehicles. FOCUS talks to some industry experts about a few ways to reduce down time.
Nothing can dampen the spirit of a new year quite like a vehicle breakdown just when business is picking up. As the transport industry gets back into high gear, it is the optimal time to ensure that the vehicles in a fleet are up to the task. It all starts with knowing when to service them.
Maintenance
A good starting point is to consider the manufacturer’s recommendation, as Pieter Potgieter, regional marketing manager of ZF Services South Africa, explains: “It is always advised to refer to the vehicle manufacturer’s service schedule.”
However, there are numerous technologies available on the market that can increase efficiency, extend service intervals and reduce total cost of ownership, as Johnnie Marais, GM of operations at Eqstra Flexi Fleet, points out.
“Any vehicle is subject to wear and tear throughout its lifecycle. The cost savings from implementing technologies therefore assist with the minimisation of wear and tear,” he says.
He emphasises that, with the correct technology in place, manufacturers are able to extend service intervals and many are even doubling service intervals.
Warning signs
While most professional transport companies have rigid maintenance plans for their vehicles, it is inevitable that there will be a need for unplanned maintenance. Very often there are warning signs to indicate a potential unplanned service. Potgieter notes that oil leaks are one of the most common indicators of faults. Transport operators should also look for vibrations and overheating.
“Blocked breathers can over pressurise the unit and blow seals. Vibrations cause brinelling within the transmission and micro movement between surfaces. Overheating could cause bearing failures, metal distortion, seal
failures and breakdown or carbonisation of the oil. An over-filled unit causes seal failure, due to the over pressurising of the unit and possible overheating,” he says.
Marais explains that some areas of the vehicle will need more attention than others. “Safety-critical items, such as towing equipment, require regular inspections and more frequent attention than the drivetrain, for example. The frequency and importance of this are operation dependant. Vehicle intelligence and machine learning is starting to become a norm whereby the robotics of the vehicle notifies the driver of any irregularities and when maintenance is required,” he states.
The Truck driver
Transport operators know that a driver has the biggest impact on the total cost of ownership. A driver influences the fuel consumption of the vehicle, the progress made on the road and is the first responder when a vehicle breaks down. Marais believes the best approach is to equip the driver accordingly and offer support when a breakdown occurs.
“It is vital to simplify the driving experience and notify the driver when finding an irregularity; as the actions taken as well as the response time will have a direct impact on the extent of the maintenance needed. It is, therefore, important to have rigid processes to equip the driver in the event of a breakdown,” he says.
However, Potgieter argues that the best approach is to prevent breakdowns. He notes: “Preventative repairs are not as costly as repairing a failed unit. When a vehicle shows possible warning signs such as strange vibrations, it is advisable to seek professional advice and understand the gravity of the problem and the potential risk involved.”
Reducing cost
While regular maintenance should reduce the total cost of ownership for companies, the experts suggest a few other ways of reducing costs.
Marais notes that inspections play an important role. “The accuracy and consistency of pre-trip and post-trip inspections are of vital importance. It is the biggest cost-saving tool in preventative and unplanned maintenance, as defects are determined before the vehicle is dispatched,” he explains.
Potgieter emphasis the importance of following the manufacturer’s recommendations: “By understanding and following the service interval recommendation of the vehicle manufacturer and making use of approved items only, such as the correct oil, a company can reduce its total cost of ownership.”
Mobile maintenance
Marais points out that the cost of maintenance is directly affected by how quickly a vehicle can be repaired or serviced. He gives an example: “A malfunctioning indicator can make a load worth R1 million stay in the yard for the day, or simply delay the deliveries. The quicker the lamp is repaired, the sooner the truck will be able to attend to all scheduled deliveries and generate revenue for the company.”
He adds that roadside assistance serves to get the vehicle back on the road as quickly as possible. There are numerous companies that offer roadside assistance or even on-site maintenance of vehicles. Eqstra Flexi Fleet offers 24-hour roadside assistance, on-site maintenance and service scheduling. ZF Services has a very similar offering.
Potgieter says: “ZF Services can assist with the maintenance of the unit fitted to your vehicle. We have highly trained field technicians who can service the transmission on site, support with diagnosing of problems, or do health inspections to assist with preventative maintenance. Our field team is geared to undertake mechanical and electrical repairs around the unit. Internal repairs will require a visit to a repair shop.”
Whether a truck is running small intercity deliveries, or hauling containers across the country, operators need to make sure it is in top shape with proper maintenance, inspections and trained, prepared drivers.
Published by
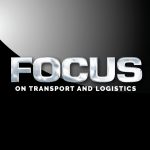
Focus on Transport
focusmagsa
