Astec cold planer breaks ground in SA
Astec cold planer breaks ground in SA
A robust and powerful machine is making waves in local road construction, setting a new benchmark for both durability and performance. The Astec RX-600ex cold planer has made its debut on the rehabilitation of Gauteng’s R21 highway, marking the first time this advanced machine has been used in South Africa – where many roads are in less-than-perfect condition.
Cold planing, or asphalt milling, is the process of removing layers of asphalt to create a smoother, more even surface for repaving. By milling away the damaged or uneven asphalt, cold planing prepares the road for resurfacing, making it safer and smoother for drivers. The amount of asphalt removed depends on both the road’s current state and the resurfacing requirements. Philip Saunders, Astec’s product sales manager for materials and infrastructure solutions, describes cold planing as a sustainable and cost-effective solution for road rehabilitation, saying that “it’s a process that can be repeated as often as needed”.
He highlights the RX-600ex’s versatility, noting that it’s ideal not only for major motorway rehabilitation, but also for urban projects. With a lighter design, it can easily manoeuvre through urban streets, allowing it to tackle lane profiling and other maintenance tasks with ease.
Engineered for power and precision
At the heart of the RX-600ex is a formidable 630-hp Cummins QSX 15 Tier III engine, driving a 2,007mm-wide QX1 asphalt milling drum with 16-mm tool spacing. This machine comes packed with features designed to enhance efficiency and ease of use. Standard inclusions range from a dust extraction system and hydraulically folding conveyor to Astec’s ACE Grade & Slope Automation system. This includes auto-cut entry, dual water spray bars, and bolt-on track pads. The quick-change cutter drum, dual-operator platform, and intuitive controls make it straightforward to operate.
According to Saunders, these features significantly benefit the operator: “A standard dust extraction system improves operator comfort and safety. The system removes dust and debris from the milling process using a hydraulic fan located at the primary conveyor. Dust is channelled out at the end of the secondary conveyor, directly into the dump truck.” This not only keeps the work environment cleaner but also ensures that dust doesn’t scatter around the site, enhancing visibility and safety.
He adds that the machine’s folding secondary conveyor further simplifies transport and loading, with a convenient “boost” function that temporarily speeds up the conveyor when handling heavier loads.
Enhanced cutter drum for simple maintenance
One standout feature of the RX-600ex is the Astec QX1 quick-change cutter drum. This design makes it easier for operators to remove and replace cutting bits and inserts. “The drum has notches in the seating face, which allows for a small wedge to remove inserts. Notches on the nose facilitate front bit removal with a fork tool,” Saunders explains. These modifications, along with shorter base blocks, allow for easier access and faster maintenance.
To minimise dust, the RX-600ex is fitted with two independent spray bars that inject water into the cutter housing. The front spray bar is primarily for dust suppression, while the rear spray bar helps to cool the milling drum, maintaining efficiency and reducing wear.
Advanced automation for consistent performance
Astec’s ACE system brings a high level of automation to the RX-600ex, enabling it to precisely calibrate hydraulic settings for consistent milling depth. This system’s grade and slope sensors ensure that each cut adheres to specified parameters, even during complex operations. New graphic displays make it easy for operators to quickly select, calibrate, and control sensors, reducing setup time and increasing efficiency.
The ACE Auto-Cut Entry system is another useful feature, as it automatically adjusts the drum’s depth at the start of a cut, rather than relying on manual adjustments by the operator. This ensures that each cut is performed at the right depth and angle.
Ergonomically designed for operator convenience
The RX-600ex’s dual-operator platform offers easy access from either side, with two control stations enabling operation from either end of the platform. Saunders highlights the simplified controls: “With multifunctional joysticks and easily accessible controls, operating the cold planer is straightforward and intuitive. Operators can control the machine with one hand, which leaves the other hand free for signalling trucks.”
Another practical feature is the bolt-on track pads, which are simple to replace and save time and money. “With traditional track pads, bolts can accumulate asphalt, making replacement a lengthy process. With the RX-600ex, the bolts are protected from asphalt build-up, so pads are quicker to change,” says Saunders.
Rock to Road: comprehensive support
The RX-600ex is part of Astec’s extensive Rock to Road range, which covers every aspect of road building, from aggregate quarrying and processing to concrete production and paving. Astec supplies more than 100 products across the aggregates, construction, infrastructure, and mining sectors, alongside global support, training, and education.
The company’s operations are divided into two primary segments. The Materials Solutions division offers solutions for handling and processing aggregates, with products including crushers, screens, apron feeders, and rock breakers. The Infrastructure Solutions division specialises in equipment for road building, including asphalt and concrete plants, as well as thermal and storage solutions.
Machines like the RX-600ex, with their high performance and fuel-saving capabilities, are particularly well-suited to infrastructure projects across Africa. With many South African roads in need of attention, the arrival of the RX-600ex represents a promising step forward for road rehabilitation and construction in the region.
Published by
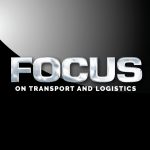
Focus on Transport
focusmagsa
