Tyres are connecting
Tyres are connecting
As the world moves into the era of digital innovation and transformation, the tyre industry is implementing new connected technologies under the umbrella of the Artificial Intelligence of Things (AIoT), a combination of AI technologies and the Internet of Things (IoT) infrastructure. This is paving the way for the transformation of vehicle maintenance and performance.
Real-time data processing of actual tyre usage helps OEMs to examine and improve existing specifications, allowing them to adjust existing and new products to specific customer circumstances. This data is also a powerful ally in end-users’ operations.
It is not by chance that, according to the latest industry research, the global smart tyre market is expected to reach a value of US$200 billion by 2033, expanding at a compound annual growth rate of 7.8% over the next decade, with the off-highway sector playing a consistent part in this growth.
More precisely, the benefits connected tyres offer in terms of predictive maintenance, operational efficiency, and long-term cost savings are driving their adoption in various demanding applications. At the same time, as technology advances, the capabilities and reliability of smart tyres are expected to improve, further solidifying their role in the future of off-highway operations.
In this complex scenario, Andrea Evangelisti, digital innovation and solutions director at Yokohama TWS (part of Yokohama Rubber), explores the evolution of digital solutions in the tyre market from Trelleborg Tires, one of the company’s brands specialising in agriculture, material handling, and construction tyres. “So far, the scenario has mainly revolved around tyre pressure monitoring systems (TPMS) – electronic systems designed to monitor the air pressure inside the pneumatic tyres of various types of vehicles, providing real-time tyre pressure information to the driver, or remotely to the fleet manager,” he says.
These solutions rely on sensors placed inside the tyre to collect data about internal pressure and temperature. The data is sent either directly to a video terminal in the vehicle, or to the cloud, before being returned for display on a selected device. “Usually, such solutions allow for the creation of reports and the recording of statistics and analytics history,” notes Evangelisti.
For example, the Trelleborg Tires TPMS system allows operators to measure pressure and temperature every five seconds, providing instant access to vehicle status and monitoring data through a computer or mobile device. Furthermore, thanks to full connectivity and cloud data transmission, the operator or fleet manager can benefit from automated email notifications in emergency situations, as well as personalised vehicle warnings.
“So far, these kinds of solutions have especially thrived in construction applications, integrating tyre sensors with a central gateway on the machine and an online platform – offering predictive maintenance capabilities, reducing vehicle downtime, and preventing accidents,” explains Evangelisti.
But what if the gathered data could also show a way to deploy adaptive solutions at full vehicle scale? For example, what if it could enable dynamic tyre pressure adjustment, based on the real load sustained by the tyre and terrain characteristics? What if vehicles could adapt other controls linked to an operation’s parameters?
“In the case of farming equipment, tyre sensing along with the soil can also be a reliable source for information gathering and automated equipment decision-making,” Evangelisti points out.
As technology has become part of the evolution of agricultural tyres, more and more producers are focusing on the effects of tyre pressure on tractor performance and soil issues like compaction. Optimal tyre pressure can increase productivity and reduce fuel consumption, all while improving crop yields and preventing damage to soil.
For this very reason, Trelleborg Tires has developed an adaptive tyre management system (ATMS), allowing tractors to always work effectively according to the application. As Evangelisti explains: “The great advantages of the ATMS, compared to a TPMS, are its new functionalities, such as the tyre dynamic load, the tractor load distribution, and the recommended tyre pressure.”
During work – and depending on the type of activity – the farmer is then constantly informed on how to optimise the tractor set-up. This encompasses the most appropriate tyre inflation pressure and ballasting for optimised traction and flotation on soil, as well as improving the set-up for road handling at lower rolling resistance.
“Consequently, while TPMS has significantly enhanced vehicle safety and reliability by ensuring proper tyre pressure, ATMS represents a further evolution in the smart tyre field. Its comprehensive approach provides real-time optimisation and predictive maintenance, ultimately offering superior safety, improved fuel efficiency, and extended tyre lifespan,” Evangelisti emphasises.
As technology advances, ATMS clearly showcases a bright future for intelligent tyre management, raising the bar for vehicle performance, soil performance, and safety in off-highway applications.
Published by
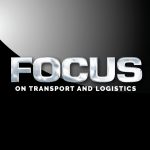
Focus on Transport
focusmagsa
